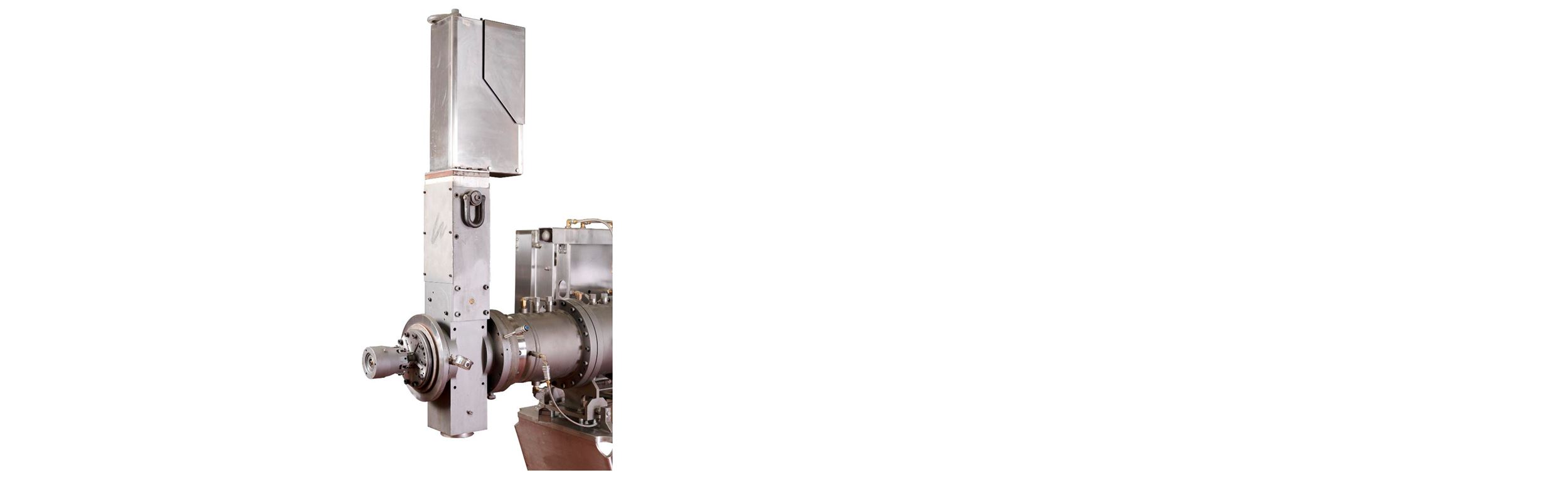
Back Pressure Valve (BPV)
Increase Control of your Extrusion Operation
The Back Pressure Valve (BPV) is a bolt-on option for your Wenger extruder that enables increased control during start-up, shut-down, and normal process operation. Three valve functions in one device make it easy to regulate pressure and peform other necessary activities.
Use during Start-Up/Shut-down:
- Divert extrudate to waste (bottom discharge)
- Eliminates wet material in knife hood or conveying system
- Cleaner work environment during start-up
- Safer work environment for shut-down and die removal
Use during Operation
- Regulate extruder barrel pressure
- Provide relief of die pressure as needed (bottom discharge)
- SME input
- Can help adjust for variations in material
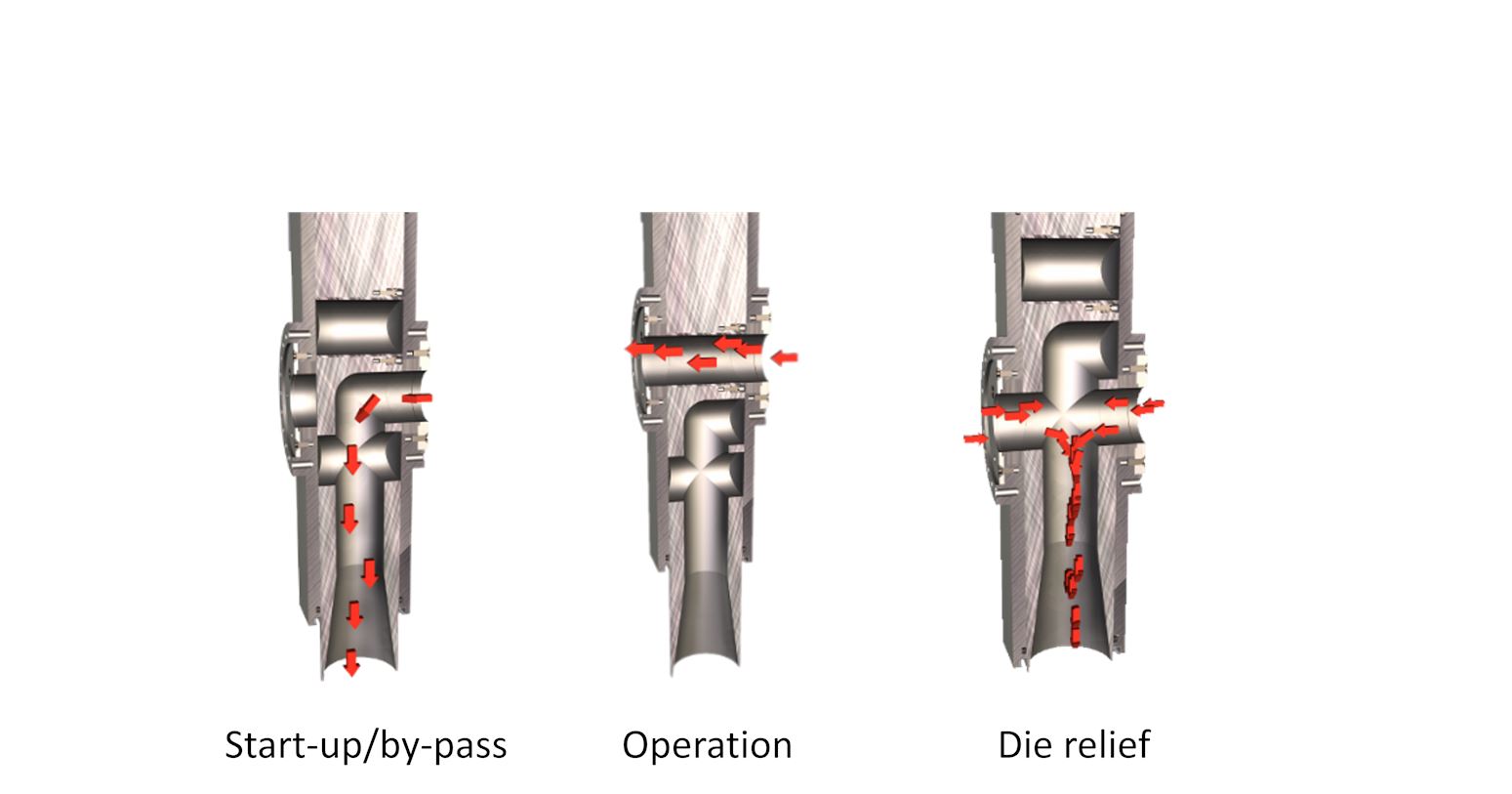
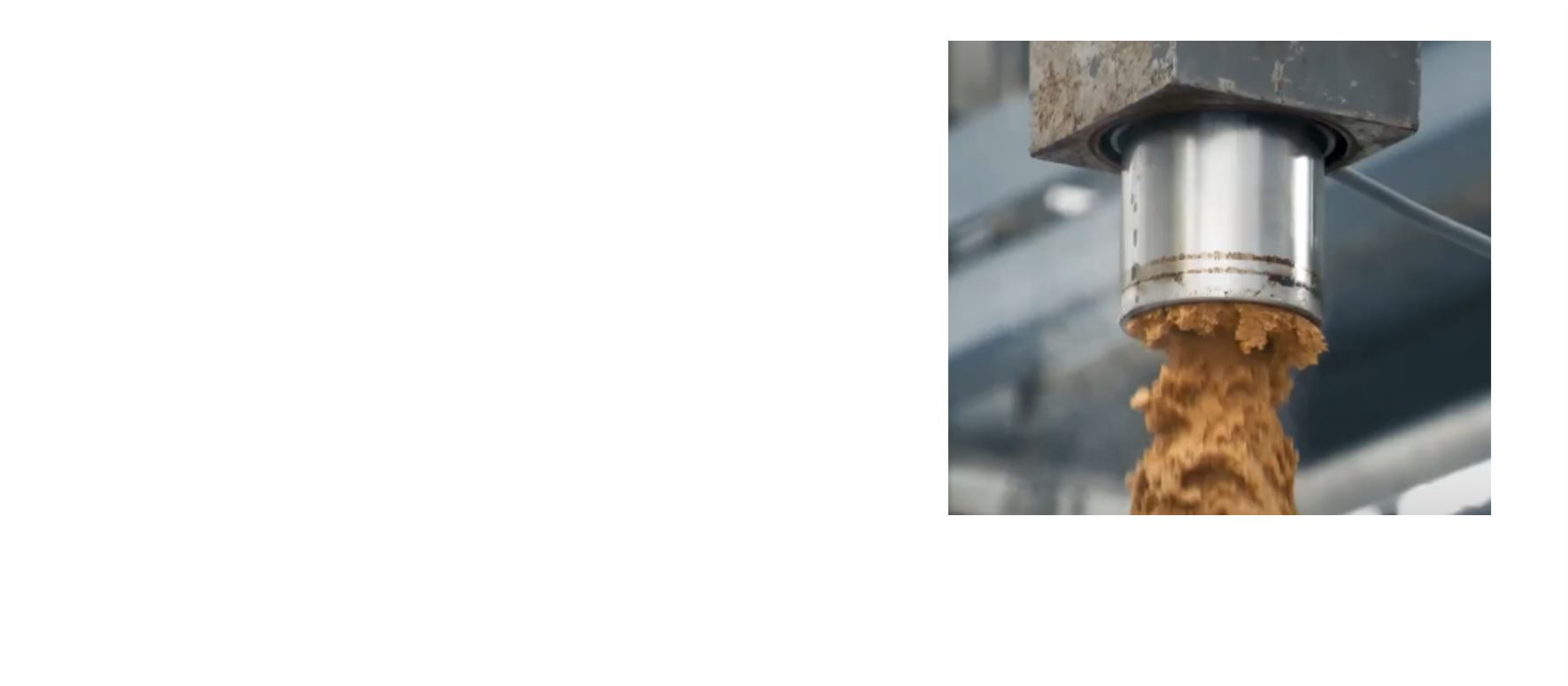
The BPV provides a vital "KILL STEP" by diverting extrudate that has not reached the CCP temperature.
Wenger systems use precision sensors in the extruder barrel that relay extrudate temperature to the control system in real time. If at any point during a production run the extrudate temperature is below the Critical Control Point (CCP) temperature, the BPV will alert the operator and switch to "discharge" mode, preventing the extrudate from entering the die. Operators can then make necessary adjustments to reach proper temperature and the BPV will return to normal operating mode (full flow to the die).
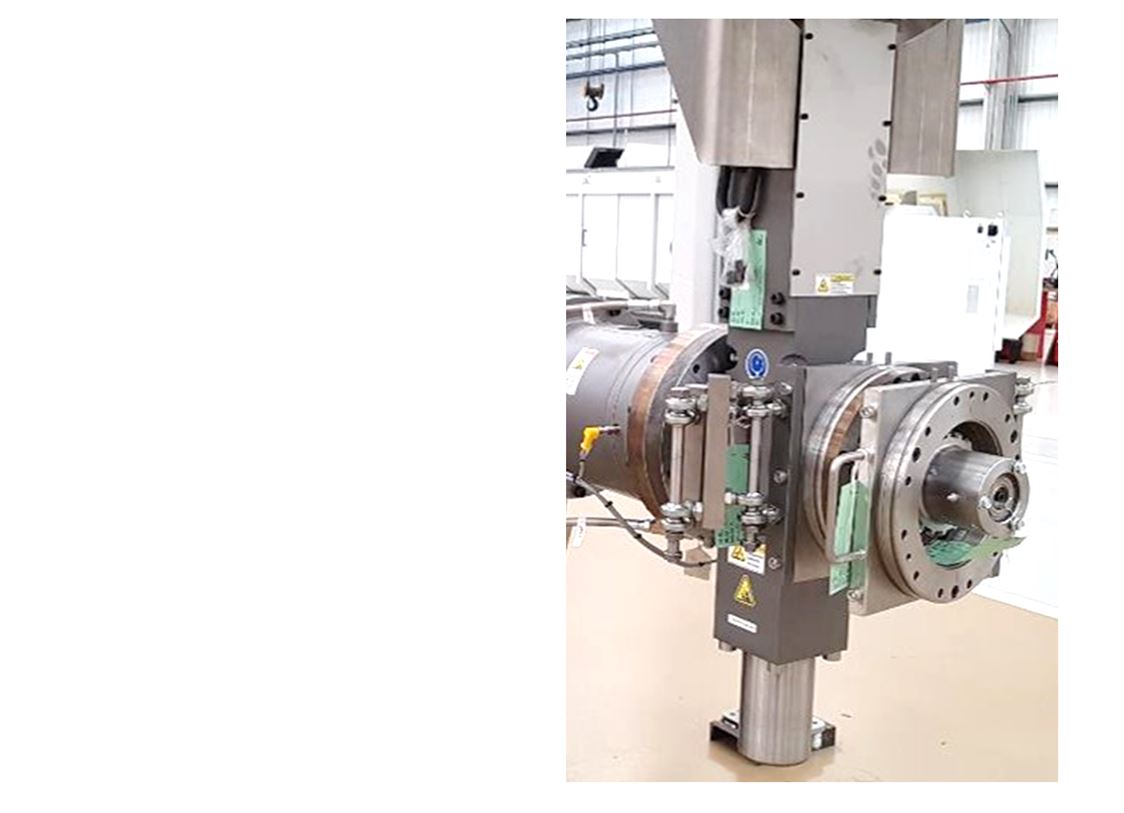
Benefits of the BPV
- Divert off-spec product for improved sanitation and quality control
- On-line adjustment of SME to control product properties (cook, density, shape, water stability, oil absorption
- Helps eliminate extruder configuration changes
- Service the die/knife/conveyor without stopping extruder
- Pressure Release – Safety!
Applications In
-
Pet Food
Traditional kibble, semi-moist, high fresh meat inclusion, treats (long, short, filled, dental) - and flexibility for new products with numerous ingredient options
-
Aquatic Feed
Floating, sinking, slow-sinking feeds, Recirculating Aquaculture System (RAS) feeds, and a wide variety of specialty feeds
Talk to a Product Specialist
to discuss the feasibility, design and implementation for your project