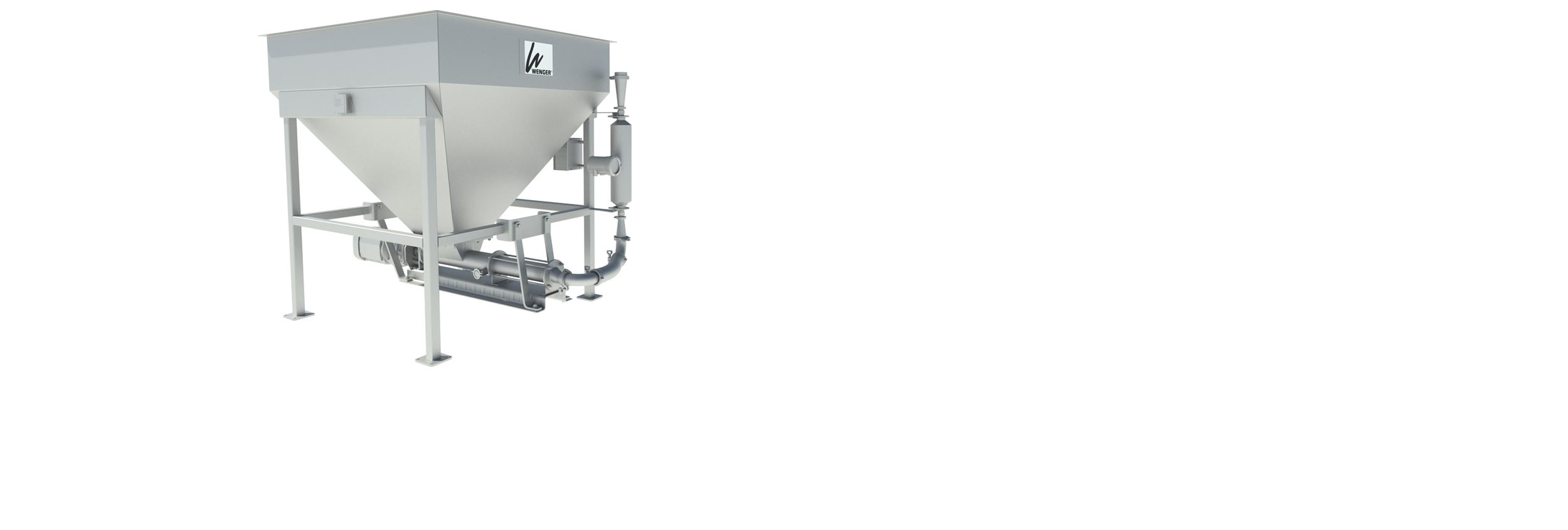
Fresh Meat Injection
Add fresh meat to high value pet foods and treats in a precise, efficient, and safe manner.
Around the world, pet parents are increasingly interested in pet foods and treats with fresh meat inclusions that increase nutrition and palatability. Wenger provides a highly engineered and customizable solution to deliver a continuous fresh meat slurry into the extrusion process. A typical Wenger solution includes a feeder bin/mixer, pumps, metering, slurry preheating, and piping to the extruder (to the preconditioner and/or the extruder barrel).
Meat System - Mixer/Pump
Typical high fresh meat inclusion system includes:
- Hopper/mixer
- Diverting screw conveyor
- Twin screw feeder(s)
- Progressive cavity pump(s) or Twin screw pump(s)
- Metering system
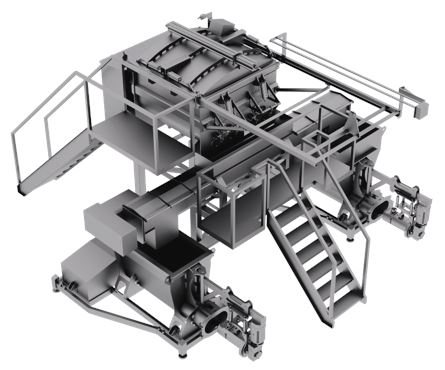
Votator - Meat Slurry Preheating
For preheating higher rates of meat slurry (>700 kg/hr), the best solution is Wenger's scraped surface heat exchanger called the Votator.
How it Works
The Votator has a tubular shaped heating chamber that surrounds an inner tube where the meat slurry is pumped through. The heating chamber contains high temperature liquid from a closed loop heating system. As the slurry passes along the tube, it is uniformly warmed to a target temperature between 40-50°C. A scraper blade moves through the inner tube to prevent meat slurry build-up and plugging. Slurry exits the Votator and is piped to the extruder preconditioner and/or barrel.
Preheated slurry is important as it enables the extruder energy to process the entire product mix to the proper temperature. In this way, the Vortator acts as a kill step enabler and can improve efficiency - especially for medium and high fresh meat content recipes.
For lower meat flow applications (<700 kg/hr), Wenger alo offers a low maintenance (no moving parts) jacketed lined tube preheater.
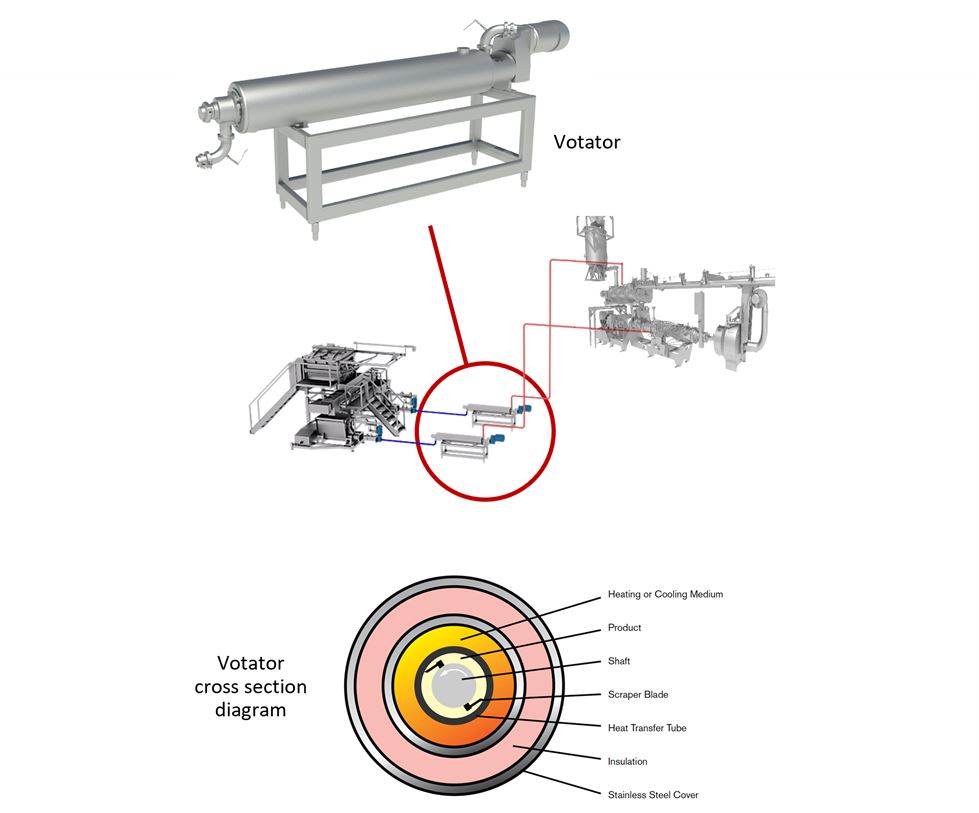
Talk to a Product Specialist
to discuss the feasibility, design and implementation for your project