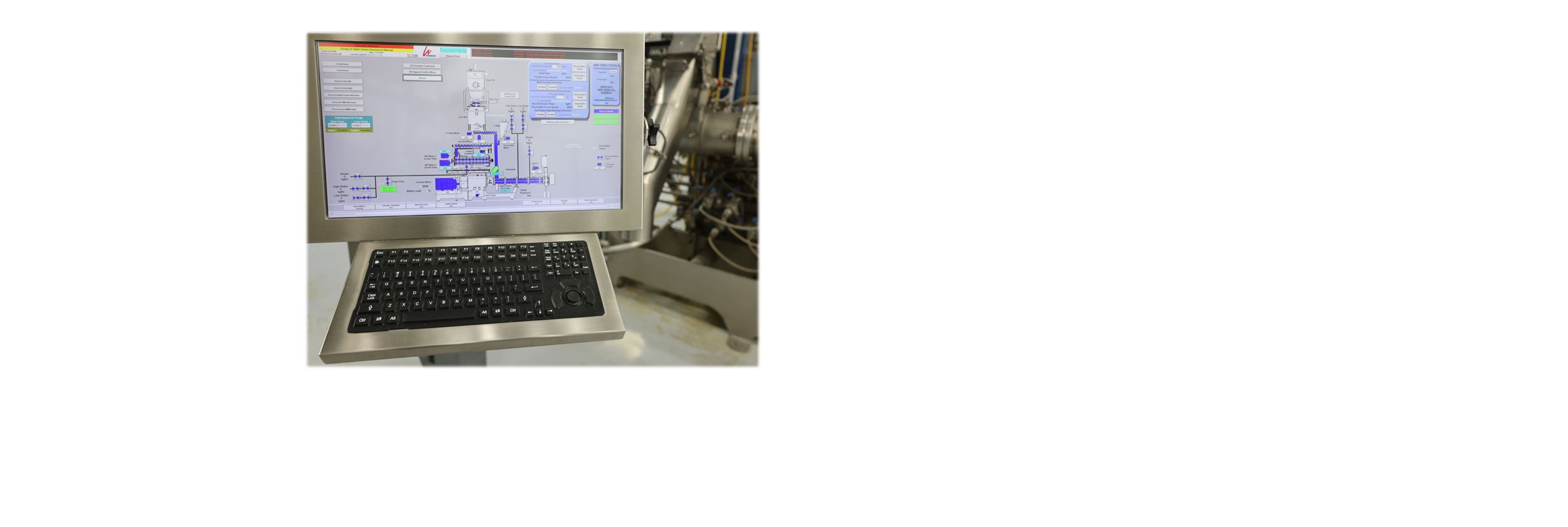
Control Systems
Easy to Use, and Designed for Safety of Products and Personnel
Wenger Automated Process Management (APM)
Process control refers to the techniques and systems used to maintain and regulate the output of a process within a desired range. It involves monitoring and adjusting various variables such as flow rate, temperature, pressure, and other factors to ensure that the process operates within established limits and produces a consistent output.
A typical Wenger APM system includes:
- Control cabinets/panels
- HMI (Human Machine Interface) screens
- Includes alarm handling, formula management, and trending
- Shortcut keys and easy-to-understand color schemes
- PLC programs
- ControlLogixTM from Allen Bradley
- Real-time control of the extrusion process and continuous process
- Software
-
Pre-programmed sequences for automatic startup, shutdown and machine cleanout
-
On-line operator adjustment of processing conditions for product fine-tuning
-
Alarms to alert operator of off-spec processing conditions
-
See the Full Picture of Equipment Operation
The Wenger APM approach provides you complete control of system operation while the equipment is running. Color coding of different process areas enables you to quickly see which areas are operatonal - and which are not. APM screens can be used to monitor and control:
- Density Control (requires Bulk Density System and Back Pressure Valve)
- Mix Intensity (requires Mix Intensity Control and High Intensity Preconditioner
- Steam Mixing Injection
- Extruder - overall
- Extruder - barrel detail
- Extruder - cleaning
- Live Bins
- Liquid Levels
- Dryers
- Dryer Speader
- Coolers
- Alarms
- All activity level on the HMI
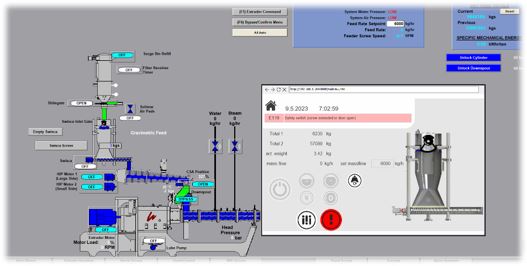
Benefits of the Wenger APM full system
- Interactive HMI of All equipment
- 10,000 Formulas (recipes)
- Product Tracking for Food Safety
- Data Logging to ERP/Database **
- Real Time Process Trending
- Wenger VFD Integration
- System Security Profiles
- Spreader Control
- Energy Control **
- Moisture Control **
- Product Matrix Control
- Remote Support
- Ease of adding future Wenger APM widgets
**optional upgrade
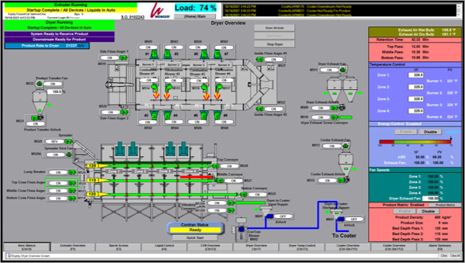
-
INSTALLATION
Pre-plumbed and pre-wired installation module reduces installation time and ensures proper connections for faster commissioning. All components are connected with the control panels for testing at our factory before shipment to identify any faulty devices or wiring mistakes.
-
TRACKING AND RECORDING
- Display and record temperatures at critical points in the system and log them by date and time for traceability
- Determine the time required to reach equilibrium temperature and critical control point (CCP) temperatures in order to better manage energy use and product hygiene
-
INTEGRATED SAFETY WITH ZONE CONTROL
Wenger's APM system enables you to create zones to prevent operation of equipment for times of cleaning, maintenace, or other purposes. For example, operation the ingredient feed system and pre-conditioner may be allowed while at the same time disabling operation of the extruder or dryer. This feature is critical to ensure personnel safety when equipment requires manual attention.
Wenger systems are designed with safety as a priority. Design details such as limiting electronics/electrical equipment in wet areas are standard for a Wenger system.
-
DATA LOGGING AND REPORTING
The APM system enables advanced data logging from the PLC into an SQL database. Detailed and customzied reports can be generated easily to help you monitor your system and identify focus areas. The server can be equipped with an unterrupted power supply (UPS) and you can also enable remote access/sevice from Wenger.
These (optional) remote services can include:
- Scheduled weekly maintenance (including relauch of server)
- Health checks of PLC
- Data back-up
Applications In
-
Food
Textured vegetable proteins, structured meat alternatives, ingredients, protein crisps, breadings, RTE cereals, snacks, hybrid products, and many more
-
Pet Food
Traditional kibble, semi-moist, high fresh meat inclusion, treats (long, short, filled, dental) - and flexibility for new products with numerous ingredient options
-
Aquatic Feed
Floating, sinking, slow-sinking feeds, Recirculating Aquaculture System (RAS) feeds, and a wide variety of specialty feeds
-
Industrial
With Wenger systems, you can create new products for industrial or consumer applications. Whatever idea you're thinking about, Wenger can help.
Talk to a Product Specialist
to discuss the feasibility, design and implementation for your project