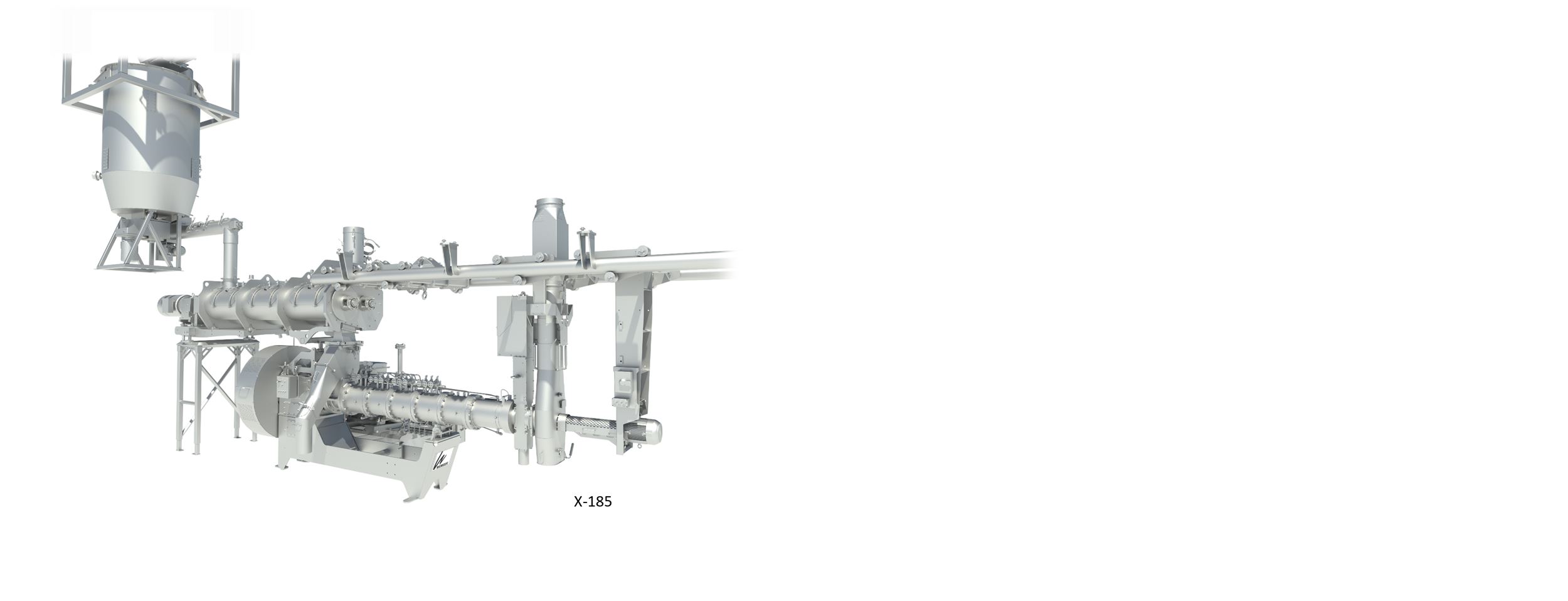
Optima Single Screw Extruders
Engineered for Performance, Productivity, Efficiency & Return
More than 40 years of experience have resulted in refinements to Optima Single Screw Extruders. Today, these extruders assure greater production potential with more available energy through the unique design of the screw flighting and barrel ribbing.
-
30% to 50% increase in production capacity
-
Improved control of product textural attributes and bulk density
-
Reduced sensitivity to component wear
-
Improved mechanical energy utilization
More available energy for more output
We re-engineered the extruder's drive components and preconditioning assembly, without compromising extruder control capabilities, finished product quality, ease of operation, or life of critical extruder components. Greater production output results in reduced capital equipment cost per unit of throughput.
-
Preconditioning Options
Wenger's Optima extruders are compatible with several preconditioner models including
- High Intensity Preconditioner (HIP) - the most advanced mixing control on the market for food, snacks, premium pet food, treats, and engineered aquatic feed
- High Shear Conditioner (HSC) - tapered design ideal for feed production
- DDC - twin shafts rotating at different speeds for production of traditional kibble and feed
-
Stainless Steel Pneumatic Product Pick-up Hood
The Product Pick-up Hood assures cleaner operation by removing waste steam, vapors and fines at the extruder discharge. The product is transported gently by negative air directly from the die to the dryer, minimizing product distortion. An access port permits samples to be drawn for examination without diverting flow or risk of injury. Remote or PLC activated diverter valves incorporated in the design facilitate extruder start-up and shut-down by allowing waste products to bypass air transport to the dryer.
-
Mid-Barrel Valve
The Mid-Barrel Valve permits SME to be increased by up to 50% while allowing more precise control of the process. Because it is an internal component, it can be installed in any position along the length of the barrel.
-
Barrel Components
Barrel components — screws, barrel sleeves, and shearlocks — are proprietary stainless steel alloys. The result is greater resistance to wear, increased barrel life and significant reductions in extruder maintenance and operating costs.
-
Back Pressure Valve
The Back Pressure Valve mounts on the end of the extruder prior to the final die and provides on-line control of shear stress and SME for regulation of product characteristics, including: size and uniformity of cell structure, shape definition, starch gelatinization, bulk density and liquid absorption.
Applications In
-
Pet Food
Traditional kibble, semi-moist, high fresh meat inclusion, treats (long, short, filled, dental) - and flexibility for new products with numerous ingredient options
-
Aquatic Feed
Floating, sinking, slow-sinking feeds, Recirculating Aquaculture System (RAS) feeds, and a wide variety of specialty feeds
-
Industrial
With Wenger systems, you can create new products for industrial or consumer applications. Whatever idea you're thinking about, Wenger can help.
Performance
Model No. | Screw Diameter | Motor kW | Capacity kg/h |
---|---|---|---|
X-115 | 115 mm | 75-132 | 500-2000 |
X-165 | 165 mm | 90-250 | 1000-6000 |
X-185 | 216 mm | 160-630 | 2000-14000 |
X-235 | 235 mm | 315-750 | 4500-20000 |
X-280 | 280 mm | 750-1000 | 20000-30000 |
Talk to a Product Specialist
to discuss the feasibility, design and implementation for your project